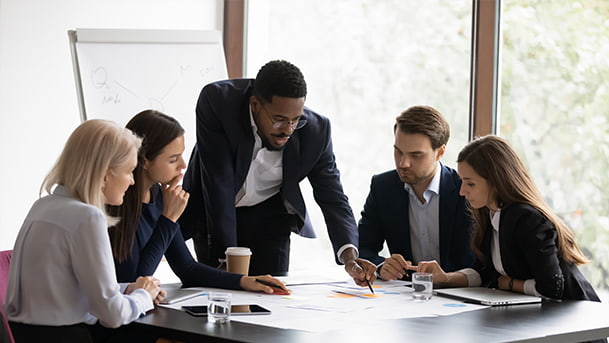
Pour faire face au changement et à la concurrence accrue, les entreprises doivent se transformer et améliorer leur processus internes. L’amélioration continue est une démarche de plus en plus plébiscitée par les entreprises pour réaliser des changements en douceur avec des résultats concrets tout en obtenant une forte adhésion des collaborateurs.
Certaines entreprises sont matures sur le sujet quand d’autres ont une forte marge de progression. Mais toute entreprise souhaite toujours s’améliorer pour gagner plus de parts de marché, être plus performant et efficace, réduire les coûts et gaspillage.
Nous vous présentons dans cet article les avantages de la mise en œuvre d’une démarche d’amélioration continue, les clefs de succès et les principales méthodes et outils.
Qu’est-ce que l’amélioration continue ?
L’amélioration continue est l’un des 7 principes de management de la qualité de la norme ISO 9001. Faire de l’amélioration continue c’est avoir la volonté d’augmenter la performance interne de l’entreprise, réduire les dysfonctionnements des processus, éliminer les gaspillages, maîtriser les risques et augmenter la satisfaction des clients. Il s’agit d’une démarche qui doit être un objectif permanent au sein de l’entreprise.
Le principe de l’amélioration continue est souvent représenté par un cycle d’actions dit cycle PDCA ou « roue de Deming », avec les 4 étapes suivantes :
P = Planifier : l’entreprise prévoie et planifie ce qui doit être réalisé en termes de processus et d’activités pour améliorer la qualité des services et produits et, ainsi, la satisfaction des clients.
D = Déployer : l’entreprise expérimente la solution qui a été sélectionnée.
C = Contrôler : l’entreprise vérifie et contrôle que ce qui a été réalisé est conforme aux objectifs fixés. Dans cette phase, elle évalue l’écart entre les objectifs fixés et les résultats obtenus.
A = Agir : l’entreprise intègre les changements à son processus opérationnel et met en place un suivi de la performance.
Pourquoi adopter une stratégie d’amélioration continue ?
Pour pouvoir s’améliorer, l’entreprise doit fixer un cadre et c’est le rôle de cette démarche. Représentée par la « roue de Deming », l’amélioration continue est une itération de cycle d’actions bien définies pour optimiser les processus opérationnels de l’entreprise.
Les intérêts de la mise en œuvre d’une démarche d’amélioration continue sont nombreux.
Un changement progressif pour une meilleure conduite du changement
L’amélioration continue consiste à mettre en œuvre des actions et tâches faciles à réaliser pour transformer les processus de manière progressive. En utilisant la méthode du cycle PDCA, les changements vont se faire par étape sans déstabiliser l’organisation. Plus simple à appréhender, vous obtiendrez une plus forte adhésion des collaborateurs qui peuvent avoir tendance à résister au changement, surtout s’il est important et brutal.
La résolution rapide des problèmes, une opportunité d’amélioration
L’amélioration continue permet de détecter rapidement des dysfonctionnements liés aux processus organisationnels de l’entreprise. En identifiant les problèmes, l’entreprise peut ainsi mettre en œuvre des actions pour les résoudre. C’est une opportunité d’amélioration.
La réduction du gaspillage
L’amélioration continue permet de détecter les gaspillages c’est-à-dire toute activité qui n’apportent aucune valeur et qui peuvent être supprimées du processus tels que le temps d’attente, la surproduction, les déplacements, les défauts tels que les bugs applicatifs, et toute tâche sans valeur ajoutée.
Supprimer ces gaspillages permet d’accroître la productivité et l’efficacité. Ces changements sont réalisés de manière progressive et sont moins coûteux que de transformer l’entreprise à grande échelle.
La motivation des équipes
Mettre en œuvre une démarche d’amélioration continue permet de mobiliser les collaborateurs de l’entreprise vers un objectif commun par la mise en place d’actions permettant de gagner en efficacité, en productivité et en sérénité. Ainsi, l’entreprise apporte une culture d’amélioration continue sur le long terme et le cycle PCDA permet de résoudre rapidement des dysfonctionnements sur le court terme.
Une meilleure visibilité
Avec l’amélioration continue, l’entreprise donne de la visibilité à chaque étape de la démarche : planification des actions, la réalisation, les résultats obtenus et les actions correctives à réaliser. En ayant cette visibilité, les collaborateurs sont engagés tout au long du processus d’amélioration continue. L’entreprise instaure une culture d’entreprise permettant d’accroitre la productivité et un environnement de travail plus serein et motivant.
Comment réussir le processus d’amélioration continue ?
L’implication de la direction
Pour que l’amélioration continue fonctionne, l’implication de la direction est fondamentale. Elle doit porter la démarche, la déployer et faire adhérer les collaborateurs de l’entreprise. Certaines entreprises n’hésitent pas à faire appel à un manager externe tel qu’un manager de transition qui sera responsable de la mise en œuvre de la démarche d’amélioration continue.
L’implication des collaborateurs
L’implication de la direction ne suffit pas. L’adhésion des collaborateurs est un des clefs du succès de la démarche. Pour ce faire, l’entreprise doit identifier en amont les freins et la résistance au changement, qui est toujours source d’inquiétude. Présentez le projet, faites-en sorte que vos équipes comprennent et perçoivent les intérêts de cette démarche d’amélioration continue : meilleure performance, élimination des tâches non utiles pour plus d’efficacité, meilleure ambiance au sein de l’entreprise, plus de sérénité, etc.
Les collaborateurs doivent comprendre leur rôle et leur contribution pour pouvoir y adhérer pleinement et ainsi être dans la recherche continuelle de progrès avec l’organisation.
Quelques méthodes et outils de l’amélioration continue
La démarche Kaizen
Le mot Kaizen est la contraction de deux mots japonais. Kai pour « changement » et Zen pour « meilleur » ou « vers le meilleur ». Le principe de cette démarche est de réaliser de petites améliorations de façon continue et graduelle, permettant une forte adhésion des collaborateurs.
Kaizen n’est pas une méthode à proprement parlé mais plutôt un état d’esprit. Des méthodes peuvent s’inscrire dans cette démarche comme le PDCA (« roue de Deming ») ou encore la méthode 5S.
La méthode 5S
La méthode 5S a été créée pour la production des usines Toyota. Cette méthode résume les 5 actions essentielles pour optimiser l’espace de travail et améliorer son environnement :
- Serei (Débarrasser) : se débarrasser du superflu, jeter ce qui n’est pas régulièrement utilisé ;
- Seiton (Ranger) : ranger l’espace de travail, classer et ordonner pour avoir chaque chose à sa place ;
- Seiso (Nettoyer) : nettoyer l’espace de travail et les outils de production pour éviter les dysfonctionnements et améliorer la sécurité ;
- Seiketsu (Maintenir l’ordre) : une fois que le superflu est jeté, que l’espace de travail est rangé, classé et ordonné, il faut continuer à maintenir l’ordre ;
- Shitsuke (Être rigoureux) : pour être efficace, il est important de continuer à respecter les 4S précédents de manière rigoureuse et durable.
L’objectif de cette méthode est de permettre aux collaborateurs d’avoir un espace de travail optimisé et serein où il est facile de retrouver les informations. Tout est à sa place ce qui permet de gagner en efficacité (plus de perte de temps pour retrouver des documents) et de réduire les accidents de travail. Bien entendu, tous les collaborateurs de l’entreprise doivent adhérer la méthode pour qu’elle fonctionne.
La méthode Six Sigma
La méthode Six Sigma a été inventée par Motorola en 1986. L’objectif est d’améliorer la qualité de production en visant le zéro défaut par l’optimisation des processus de l’entreprise. Cette méthode est décomposée en 5 étapes cyclique :
- Étape 1 – Définir : cette étape du processus d’amélioration défini les attentes du client et permet de détecter les problèmes à résoudre. Les entreprises peuvent se baser sur des études qualitatives pour comprendre les besoins du client, leur motivation et leur comportement.
- Étape 2 – Mesurer : durant cette étape, l’entreprise évalue la performance du processus actuel en récoltant des données. Pour ce faire, des études quantitatives tels que la satisfaction client peuvent être réalisées afin de récupérer des données chiffrées et ainsi mesurer la performance du processus.
- Étape 3 – Analyser : cette étape permet d’analyser les processus et les données collectées et réfléchir à des actions d’amélioration ;
- Étape 4 – Améliorer : durant cette étape, l’entreprise met en œuvre les solutions pour résoudre les problèmes détectés et améliorer le processus.
- Étape 5 – Contrôler : l’entreprise vérifie que les solutions mises en œuvre correspondent aux objectifs fixés et aux attentes du client. Pour ce faire, un plan de surveillance avec des données mesurables doit être mis en œuvre.
La méthode « juste à temps »
Principalement utilisée dans la gestion des approvisionnements, la méthode du juste à temps consiste à s’approvisionner des matières premières ou tout élément à assembler qu’à la réception des commandes clients afin d’éliminer les stocks inutiles et ainsi le gaspillage. Pour être efficace, cette méthode doit être adoptée par les clients et les fournisseurs. L’entreprise doit pouvoir mener plusieurs actions d’optimisation tels qu’une estimation fiable des besoins de production, une stricte gestion des stocks et des commandes, un approvisionnement local permettant de réduire les délais et les coûts, etc.
Les cercles de qualité
Il s’agit d’une méthode de travail d’origine japonaise qui consiste à réunir de façon périodique un groupe de personnes pour échanger sur des problématiques. Les personnes regroupées sont directement concernées et sont les mieux placées pour analyser, diagnostiquer et proposer des solutions adaptées.
Il s’agit d’une approche collaborative et participative dont les objectifs sont d’augmenter la productivité, réduire les gaspillages, améliorer l’organisation du travail et la communication au sein de l’entreprise. Ces ateliers sont l’occasion d’échanger sur les expériences, détecter les axes de progression notamment par la formation et proposer des idées innovantes. Les collaborateurs qui participent à cette méthode adhèrent plus facilement au changement.